Get Your Shop Lean – Implementing Six Sigma
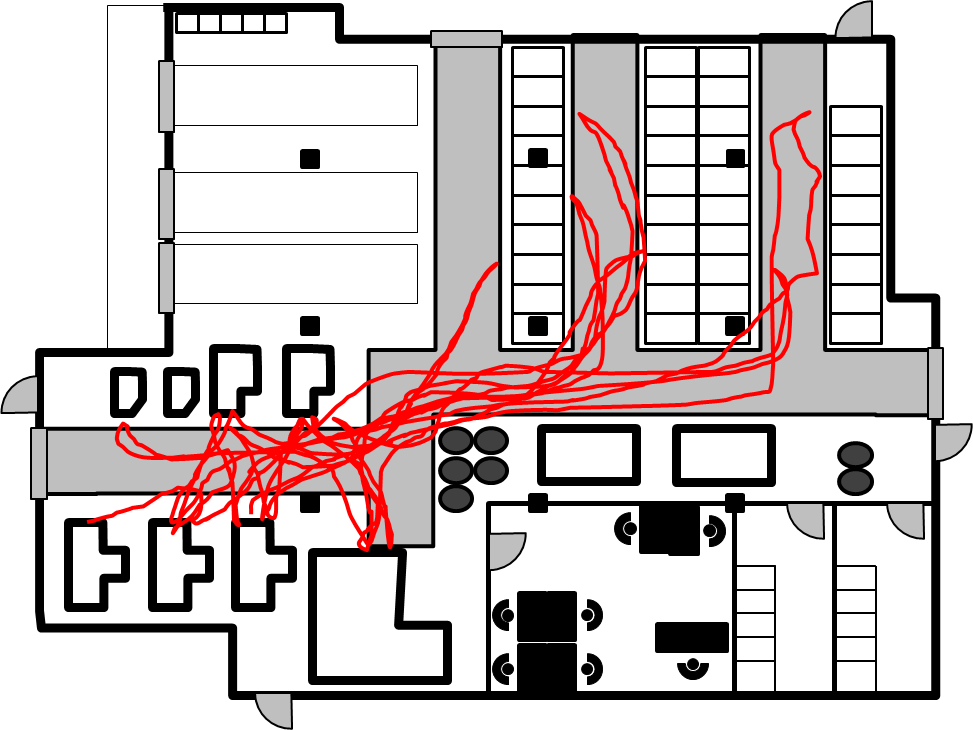
I believe that taking a deep dive into your procedures will become an important strategy to growing a stronger business. What if you were able to find three or four minutes per procedure? Think about how many brake jobs or oil changes you do. Multiply the time savings by the number of jobs you do and you’ll soon see that you can add time back into your day. We sell time and when we waste it, we never get it back.
We’ve recently done a few shows on lean. A recent Town Hall Academy really shows how this business strategy will work in your business. Here is the link.
Six Sigma Lean is a statistical process improvement methodology that uses a set of tools to identify and eliminate the causes of defects in manufacturing and service processes.
It is a process improvement strategy that uses simple statistical tools to detect, analyze and isolate defects in order to continuously improve products, processes, and services.
The Six Sigma Lean approach is a statistical and methodological approach to company management. It follows the principles of lean manufacturing and Six Sigma in order to achieve a high-quality product or service at reduced costs by eliminating defects (think comebacks).
Simply put you can review every procedure you have in your shop. You involve your team and discover all the steps, tools, people, systems, you need to perform said task.
A great example used in our podcast is the ‘Oil Change’. The opportunity to deeply review what we do when we have an oil change, where the tools are, where are the filters, among others. How many steps do we take to do one of the most repetitive tasks we have in our shop.
I believe this will be a top-five critical strategy in your business, up to and including growing sales, building leaders, succession planning, and financial controls.
You must give this podcast a listen so you can learn and appreciate the value and power of making your procedures ‘Lean’. Pull the team together to listen or watch this episode.
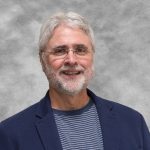
About the author, Carm Capriotto, AAP
Carm is the founder and host of the Remarkable Results Radio Podcast and the pioneer of automotive aftermarket podcasts. Carm calls on his years of experience in the aftermarket to bring engaging stories from his guests.
Listen to raw, unfiltered, honest, and sincere stories that include insights, trends, best practices, and expertise. Each interview brings an opportunity to learn one new thing through the stories of personal achievement. Many podcast guests tell their story of transformation from working in their business to working on it.
As host of over 1,000 episodes, Carm uses his enthusiasm and passion for the aftermarket especially the service sector to take his listeners on a journey showcasing successful service professionals’ paths to Remarkable Results. He also enjoys interviews with aftermarket industry thought leaders who bring their industry perspectives to his listener.
Follow the podcast on your favorite podcast listening app and always listen to learn just one thing!